Flare Vaporizers typically operate in conjunction with the
user’s Overhead Flare Drum to vaporize near atmospheric pressure liquid which
arrives at the Drum and needs to be immediately flared. In the case of Ethylene
the material is typically vaporized at a temperature of approximately (-101° C/
-149.8° F).
Circulation of the Cold Process Liquid between the Drum and the Flare Vaporizer
is by natural thermosiphon recirculation caused by the liquid bead acting from
the Overhead Drum. The unit typically boils a portion of the liquid entering the
Vaporizer; any excess liquid returns to the Drum with the vapor via riser
piping, and then recirculates back to the Vaporizer.
Armstrong Chemtec Group designs have been proven over many
years of successful operation. Significant design considerations include the
following;
-
Response Time - Units are very responsive, i.e. able to adjust
more or less immediately to process changes from 0 to 100% of design load.
-
Flexible Coil Construction - This produces minimum levels of
thermal stress and minimum potential for fatigue failure.
-
Freeze Proof Construction - Steam condensate is maintained well
above the freeze point of water by proper deployment of internals, proper
venting of inerts and proper removal of steam condensate.
-
Materials of Construction - These include Carbon Steel, various
300 Series Stainlesses, Nickel Alloys include Inconel 600 and Incoloy 825 and
many other weldable materials suitable for specific design conditions.
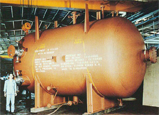
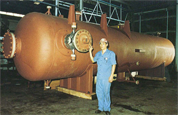
|