Armstrong Chemtec Group, having its parent company, Armstrong Engineering Associates, Inc., in Pennsylvania in the
U.S.A. and its wholly owned subsidiary, Chemtec UK Ltd., in Beith in
Scotland, is specializing in Process Heat Transfer.
For over 70 years, Armstrong Chemtec Group has been designing and manufacturing
heavy duty industrial equipment for some of the most demanding and hazardous
processes in the Chemical, Petrochemical and Oil Refining Industries and has
supplied the same globally.
Direct Steam Heated Vaporizers of horizontal shell and coil construction
for Hydrocarbons, Cryogenic and Hazardous Fluids:
For cryogenic applications Armstrong Chemtec Group offers
Direct Steam Heated Vaporizers of horizontal shell and
coil construction.
The vaporizing process fluid passes through the inside of the coil and the
steam, used as the heating medium, is in the shell. This type of construction is
normally offered for fluids such as Ethane, Ethylene, Nitrogen and frequently
Hydrogen Chloride. However, the possibility exists to use Armstrong
Chemtec Group’s shell and coil units for other fluids boiling at
temperatures less than the freezing point of water. Armstrong Chemtec
Group’s unique equipment is designed and proven free of freeze-up
problems for process fluid boiling temperatures as low as the atmospheric
boiling temperature of nitrogen (-190° C/ -320° F). Many of such units are in
olefin process service and fall into either of the following applications, each
of which demands high reliability.
Armstrong Chemtec Group designs have been proven over many
years of successful operation. Significant design considerations include the
following;
-
Response Time - Units are very responsive, i.e. able to adjust
more or less immediately to process changes from 0 to 100% of design load.
-
Flexible Coil Construction - This produces minimum levels of
thermal stress and minimum potential for fatigue failure.
-
Freeze Proof Construction - Steam condensate is maintained well
above the freeze point of water by proper deployment of internals, proper
venting of inerts, and proper removal of steam condensate.
-
Materials of Construction - These include carbon steel, various
300 series stainlesses, nickel alloys include Inconel 600 and Incoloy 825, and
many other weldable materials suitable for specific design conditions.
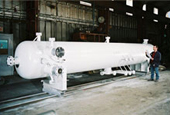
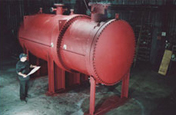
Vertical Bayonet Vaporizers:
Armstrong Chemtec Group designs and manufactures
Vertical Bayonet Vaporizers used to generate vapor from materials
stored as liquids but used in downstream processes as vapor. These most
frequently use steam or hot water as the heating medium, for which the vaporizer
construction offers a degree of built-in protection against freeze-up. In
addition to steam and hot water, other heating media include glycol-water mixes
and various commercial heat transfer fluids. The vaporizing process fluid is in
the shell and the heating medium passes through the tubes. Armstrong
Chemtec Group has built approximately 4,500 Vertical Bayonet
Vaporizers for hundreds of process fluids. Some of the more common
applications are as listed below;
• Ammonia
|
• Propylene/Butene
|
• Isobutylene
|
• Di/Trichlorosilane
|
• C3-C6 Hydrocarbons
|
• Nitroethane
|
• Carbon Dioxide
|
• Silicon Tetrachloride
|
• 2,4 Toluene Diisocyanate
|
• LPG Fluids
|
• Methanol/Ethanol
|
• Trichloroethylene
|
• Chlorine Vaporizers
|
• Sulfur Dioxide
|
• Vinylidene Chloride
|
As for Chlorine, Armstrong Chemtec Group of Companies are
members of the Chlorine Institute and Euro Chlor
and have capability to meet their specific requirements.
Armstrong Chemtec Group has supplied over 1,000
Chlorine Vaporizers over the years. Not specifically listed are
vertical bayonet Regenerant Vaporizers used in widely licensed refinery
regeneration processes.
Armstrong Chemtec Group manufactures Vertical Bayonet Vaporizers using Carbon
Steel, Various 300 Series Stainlesses, Nickel Alloys including Monel and many
other weldable materials. The unique bayonet (tube in tube) construction first
used by Armstrong for this application gives rise to a number of advantages as
compared to other types of vaporizing equipment.
-
Freeze Protection - Of
importance for steam heated units is that the condensate is warmed by the
incoming steam, thus providing a measure of freeze protection. - Holdup Volume -
The retained volume of hazardous process liquid is low relative to alternative
designs. - Capacity Control - The liquid level and vaporization rate are self
regulating with downstream demand, thus simplifying controls.
-
Unlimited
Turndown - The unit can operate at turndown approaching 100%.
-
Unrestrained Tube
Expansion/Contraction - The tubes are fixed at one end only, thus free of
thermal stress.
-
Superheat - When specified at the design stage integral
superheat capability can be provided.
-
Small Foot Print – Vertical equipment
occupies significantly less plot space than horizontal options.
-
Removable
Bundle – The bundle is removable and can be replaced easily in the field.
-
Armstrong Experience - Armstrong Chemtec Group
is the worldwide leading supplier of this equipment,
based on a wealth of experience gained over 70 years of designing and
fabricating vaporizers from plants in the USA, Scotland and Singapore.
Armstrong Chemtec Group also
designs and manufactures horizontal direct electric and horizontal indirect
electric vaporizers for various applications.
|